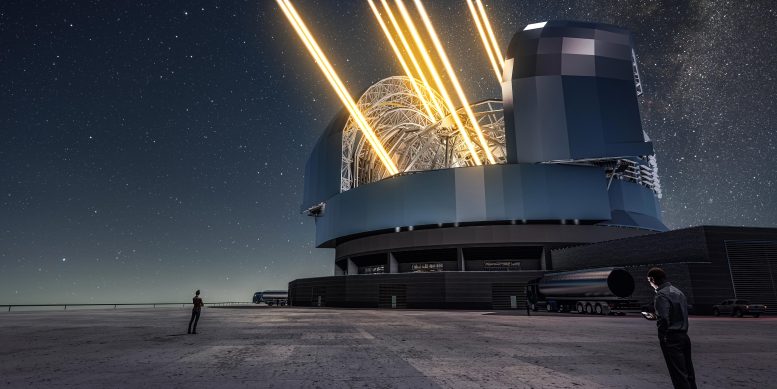
This artist’s impression shows a nighttime view of the Extremely Large Telescope in operation on Cerro Armazones in northern Chile. The telescope uses lasers to create artificial stars in the upper atmosphere. Credit: ESO/L. Calçada
Successful casting of the last mirror segment of the world’s largest telescope
The Chilean Giant Telescope, which is expected to be completed in the next decade, will be the largest telescope in the world, with a 39-meter-long main mirror made up of 798 precision segments. It represents a major international effort in the field of astronomy.
Currently under construction in the Chilean Atacama Desert, the European Southern Observatory’s Extremely Large Telescope (
” data-gt-translate-attributes=”({“attribute”:”data-cmtooltip”, “format”:”html”})” tabindex=”0″ role=”link”>ESOThe ELT is nearing completion. The German company SCHOTT has successfully delivered the draft of the last of the 949 segments ordered for the telescope’s primary mirror (M1). With a diameter of over 39 meters, M1 will be by far the largest mirror ever manufactured for a telescope.
Innovations in telescope mirror design
Too large to be made from a single piece of glass, M1 will consist of 798 hexagonal segments, each about five centimetres thick and 1.5 metres wide, that will work together to collect tens of millions of times more light than the human eye. An additional 133 segments have been produced to facilitate maintenance and coating of the segments once the telescope is operational. ESO has also purchased 18 spare segments, bringing the total number to 949.
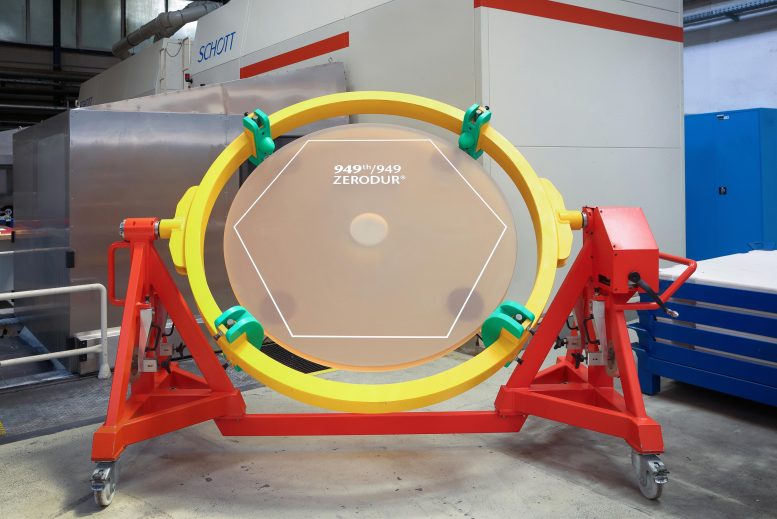
The primary mirror for ESO’s Extremely Large Telescope (ELT), called M1, will be by far the largest mirror ever made for a telescope. With a diameter of over 39 metres, M1 is too large to be made from a single piece of glass. It will consist of 798 hexagonal segments, each about five centimetres thick and 1.5 metres wide, which will work together to collect tens of millions of times more light than the human eye. An additional 133 segments have been produced to facilitate maintenance and coating of the segments once the telescope is operational. ESO has also purchased 18 spare segments, bringing the total number to 949. The German company SCHOTT has now successfully cast the last of the 949 segments, shown in this photo. The M1 blanks, shaped pieces of material that are then polished to become the mirror segments, are made of ZERODUR©, a low-expansion glass-ceramic material developed by SCHOTT and optimized for the extreme temperature ranges of the ELT site in the Atacama Desert. The 949th segment is seen in this image before being cut into a hexagonal shape and polished, steps that will be carried out by the French company Safran Reosc. Credit: SCHOTT
Advanced materials and production techniques
The M1 blanks, shaped pieces of material that are then polished to become the mirror segments, are made of ZERODUR®, a low-expansion glass-ceramic material developed by SCHOTT and optimized for the extreme temperature ranges at the ELT site in the Atacama Desert. The company also manufactured the blanks for three other ELT mirrors – M2, M3 and M4 – at its facilities in Mainz, Germany.
Collaboration and precision engineering
“What ESO ordered from SCHOTT was much more than just ZERODUR®,” explains Marc Cayrel, Head of ELT Optomechanics at ESO. “Working closely with ESO, SCHOTT refined every step of the production process, adapting the product to meet and often exceed the very strict requirements of ELT. The exceptional quality of the blanks was maintained throughout the series production of more than 230 tons of this high-performance material. ESO is therefore very grateful for the professionalism of the skilled teams at SCHOTT, our trusted partner.”
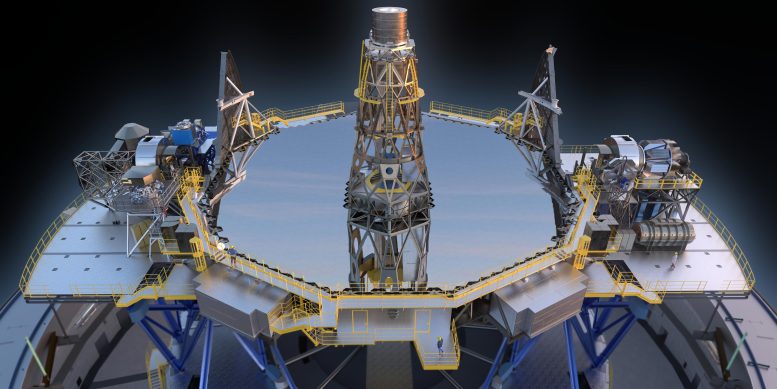
Computer rendering of the main mirror (M1) of ESO’s Giant Telescope. Credit: ESO
Thomas Werner, ELT Project Manager at SCHOTT, says: “Our entire team is delighted to conclude what has been the largest single ZERODUR® order in our company’s history. For this project, we have successfully completed the series production of hundreds of ZERODUR® mirror substrates, whereas we usually have a one-piece production. It was an honor for all of us to help shape the future of astronomy.”
International logistics and assembly
Once cast (see video below), all segments follow a multi-stage international journey. After a slow cooling and heat treatment sequence, the surface of each blank is shaped by ultra-precise grinding at SCHOTT. The blanks are then transported to the French company Safran Reosc, where each one is cut into a hexagon shape and polished to a precision of 10 nanometers across the entire optical surface, which means that the surface irregularities of the mirror will be less than one thousandth of the width of a human hair.
Also involved in the work on the M1 segment assemblies are: the Dutch company VDL ETG Projects BV, which produces the segment supports; the German-French consortium FAMES, which developed and is finalising the manufacture of the 4,500 nanometre segments.
” data-gt-translate-attributes=”({“attribute”:”data-cmtooltip”, “format”:”html”})” tabindex=”0″ role=”link”>precision sensors that monitor the relative position of each segment; the German company Physik Instrumente, which designed and manufactures the 2,500 actuators capable of positioning the segment with nanometric precision; and the Danish company DSV, which is responsible for transporting the segments to Chile.
Once polished and assembled, each M1 segment is shipped by ship to the ELT’s technical facility at ESO’s Paranal Observatory in the Atacama Desert—a 10,000-kilometre journey that more than 70 M1 segments have already completed. At Paranal, just a few kilometres from the ELT’s construction site, each segment is coated with a layer of silver to make it reflective, after which it will be carefully stored until the telescope’s main structure is ready to receive it.
Final steps and future impact
When it enters service later this decade, ESO’s ELT will be the world’s greatest observer of the sky, tackling the greatest astronomical challenges of our time and enabling discoveries never before imagined.